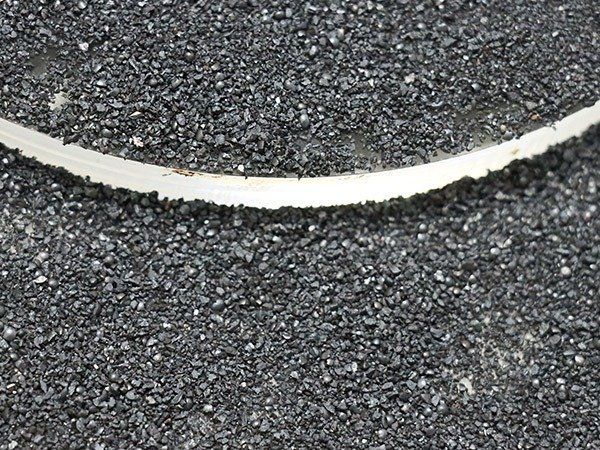
Product Description
Parameters |
|||
Product |
Steel Grit GP |
Steel Grit GL |
Steel Grit GH |
Shape |
Angular |
||
Chemical composition |
0.80%≤C≤1.20%, Si≥0.40%, 0.35%≤ Mn≤1.20% |
||
Microhardness |
40-51 HRC |
54-61 HRC |
60 HRC min |
Standard deviation |
± 3Rc (± 80 HV) |
||
Microstructure |
Uniform tempered martensite or tempered bainite |
||
density |
7.0g/cm³ |
Particle Size Distribution Table |
|||||||||||
mesh |
mm |
Specification of Steel Grit mm |
|||||||||
2.5 |
2.0 |
1.7 |
1.4 |
1.2 |
1.0 |
0.6 |
0.4 |
0.2 |
0.1 |
||
7 |
2.80 |
all pass |
|
|
|
|
|
|
|
|
|
8 |
2.36 |
|
all pass |
|
|
|
|
|
|
|
|
10 |
2.00 |
80%min |
|
all pass |
|
|
|
|
|
|
|
12 |
1.70 |
90%min |
80%min |
|
all pass |
|
|
|
|
|
|
13 |
1.40 |
|
90%min |
80%min |
|
all pass |
|
|
|
|
|
16 |
1.18 |
|
|
90%min |
75%min |
|
all pass |
|
|
|
|
18 |
1.00 |
|
|
|
85%min |
75%min |
|
all pass |
|
|
|
20 |
0.850 |
|
|
|
|
|
|
|
|
|
|
25 |
0.710 |
|
|
|
|
85%min |
70%min |
|
all pass |
|
|
30 |
0.600 |
|
|
|
|
|
|
|
|
|
|
35 |
0.500 |
|
|
|
|
|
80%min |
|
|
|
|
40 |
0.425 |
|
|
|
|
|
|
70%min |
|
all pass |
|
45 |
0.355 |
|
|
|
|
|
|
|
|
|
|
50 |
0.300 |
|
|
|
|
|
|
80%min |
65%min |
|
all pass |
80 |
0.180 |
|
|
|
|
|
|
|
75%min |
65%min |
|
120 |
0.125 |
|
|
|
|
|
|
|
|
75%min |
60%min |
200 |
0.075 |
|
|
|
|
|
|
|
|
|
70%min |
325 |
0.045 |
|
|
|
|
|
|
|
|
|
|
SAE |
G-10 |
G-12 |
G-14 |
G-16 |
G-18 |
G-25 |
G-40 |
G-50 |
G-80 |
G-120 |
Specification |
||||
G120/0.1 |
G80/0.2 |
G50/0.4 |
G40/0.6 |
G25/1.0 |
G18/1.2 |
G16/1.4 |
G14/1.7 |
G12/2.0 |
G10/2.5 (MM) |
Application |
1. Cleaning 5. Sand blasting
|
Grit Size |
Approx. Size of Abrasive |
Grit Finish Produced |
General Applications |
G-120 |
0.1mm |
Very light etch-Matte or satin finish |
Removal of very light scale Blasting of small ferrous & non-ferrous work & machine parts |
G-80 |
0.2 mm to |
Medium etch |
Blasting of small ferrous and non-ferrous castings Removal of light mill scale from forgings and heat-treated parts Removal of mill scale, rust and other deposit Powder coating, light steel, airblast |
G-25 |
1 mm |
Sharp etch |
Blasting of grey iron, malleable iron, light steel castings Pipe coating, structural steel, wheelblast |
G-18 |
1.2 mm |
Deep etch, rough |
Blasting of steel, heavy malleable iron, and grey iron castings Removal of scale from large billets, slabs or heavy rust Pipe coating, heavy structural steel, wheelblast |
G-12 |
2.0 mm |
Very rough |
Heavy steel casting Removal of tough heavy scale Bottom pour sealing application |
FAQ |
1.What is steel grit used for? Steel grit is utilized in the industrial sector for the preparation of metallic surfaces prior to the application of coatings of in desanding and descaling applications in foundries and forging. It is designed to remove existing coatings, rust, sand, scale and other contaminants, creating a clean, rough surface texture. This process enhances the adhesion of subsequent coatings, ensuring their longevity and effectiveness. 2.What is the hardness of steel grit?
Steel grit comes in various hardness levels to suit different applications. General hardness ranges from 40 to 65 HRc, 40-51 HRC is for softer applications like removing softer coatings without damaging the underlying surface, while harder steel grit, up to a minimum of 60 HRC, is preferred for more aggressive surface preparation tasks, such as removing tougher coatings or creating a profile on harder materials. 3.What is the grade of steel grit? Steel grit is categorized into different grades based on hardness. It includes GP (General Purpose) for softer grit, GL (greater hardness ranges) for a medium , and GH for the hardest grit. Each greade servers different needs and are suitable for specific applications. 4.What is the difference between steel shot and steel grit? The main difference lies in shape and application. Steel shot is spherical and ideal for peening or removing light scale and sand, while steel grit, with its angular shape, is more effective for surface preparation and cleaning application, where it can etch the metal surface to improve coating adhesion. 5.What applications are suitable for each hardness level of steel grit? The softer GP range is perfect for shot blast turbines aimed at preserving delicate surfaces. GL, being harder, is best suited for descaling, while the hardest range of steel grit, GH, proves effective in rough and heavy surface treatment processes. 6.What are the chemical compositions of different steel grit specifications? The chemical composition of steel grit typically contains carbon (C), silicon (Si), and manganese (Mn). These elements are controlled three times for each production batch to meet strict internal quality standards, ISO standards, and industry norms. The high carbon content ensures hardness and durability, whereas manganese and silicon contribute to the grit’s strength and abrasive properties. Sulfur (S) and phosphorus (P) levels are kept to a minimum to prevent brittleness in the steel. 7.can you explain the sizing options available for steel grit? Our steel grit comes in a variety of sizes, and sizing is determined by a numbering system ranging from G12 (larger, coarser particles) to G120 (smaller, finer particles). This range allows for selection based on the desired surface finish and the specific requirements of the surface preparation task, from aggressive cleaning and profiling to more delicate operations. Typical sizes include, from largest to smallest: G12, G14, G16, G18, G25, G32, G40, G50, G80, G120. 8. What do the numbers in these sizes mean? The numbers in steel grit sizes, such as G25, G40, G80, or G120, correspond to the grit’s mesh size or the number of holes per linear inch in the screen through which the grit is sized. |